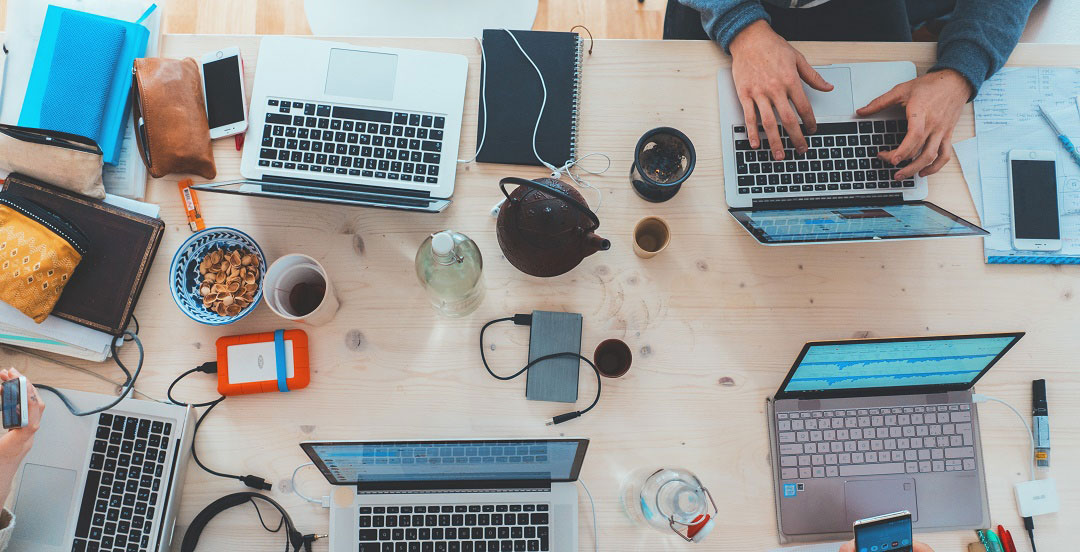
Elevating Product Durability Assessment: A Deep Dive into Advanced Testing
To guarantee the dependability and lifespan of various manufactured items, product durability testing is a crucial component of industrial quality control. The Dual Rub Tester has become a crucial tool in the arsenal of testing procedures for determining material wear and tear. This article explores the relevance of this Rub Tester, its functional principles, industrial uses, and its contribution to the development of product durability testing. Understanding this technology’s role in improving product quality and resilience requires an understanding of how it simulates real-world circumstances.
Operational Mechanism:
According to this Rub Tester’s operating theory, friction and abrasion between materials regularly occur in real-world situations. It uses two rubbing surfaces to simulate how things interact when in use. By carefully simulating the repetitive processes that items frequently go through, this device precisely measures the degree of material deterioration. The tester provides accurate insights into how items hold up over time by using various pressures and rub materials.
Significance in Product Durability Testing:
The Dual Rub Tester is an excellent tool for assessing product robustness since it can simulate real-world usage circumstances. This technique is used by sectors in the textile and electronics industries to evaluate the durability of coatings, printed patterns, fabrics, and other surface treatments. Manufacturers may optimize their production processes and increase product lifespan by studying the effects of friction, abrasion, and repetitive contact on materials
Applications in Different Sectors:
This Rub Tester has several uses in a variety of industries. It helps the automobile industry assess the interiors of vehicles for wear resistance, making sure that the materials sustain repeated usage without losing their visual appeal. A similar technique is used in the electronics industry to evaluate the robustness of touchscreens and control panels, ensuring that user interfaces will continue to be usable and aesthetically pleasing over time.
Advancements in Material Science:
This Rub Tester continues to be at the front edge of innovation as materials science advances. Researchers learn a great deal about the possible uses and constraints of novel materials by putting them through rigorous rubbing simulations. This knowledge supports the creation of innovative materials with improved durability, assisting the industry in creating goods that meet customer demands for durability and performance.
Contributing to Quality Assurance:Â
This Rub Tester is essential to quality control since it makes sure that goods meet or surpass industry requirements. Manufacturers can pinpoint weak spots in materials and make educated judgments regarding design alterations by putting samples through carefully timed rubbing cycles. This procedure not only improves the general quality of the items but also helps to reduce product recalls and warranty claims, which in turn increases consumer confidence.
Conclusion:
The Dual Rub Tester has become a key instrument in the field of industrial product durability testing for evaluating material wear and tear. Manufacturers are empowered to improve their materials and production techniques, which eventually results in more durable and long-lasting goods thanks to their capacity to simulate real-world friction and abrasion conditions. This Rub Tester is destined to be a pillar of product development and quality assurance across several sectors as technology develops, guaranteeing that customer expectations for durability are continually satisfied.